We specialise in the treatment of mine-impacted water from low pH acid rock drainage waters to excess tailings storage supernatant. Our expert process modelling capability enables us to generate overall mass balances for water treatment facilities that include:
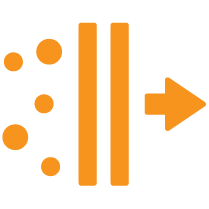
Ultrafiltration
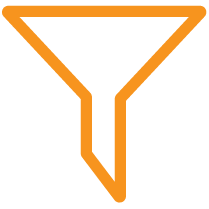
Multimedia filtration
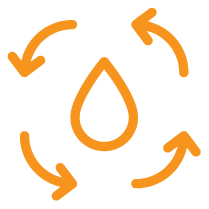
Reverse osmosis
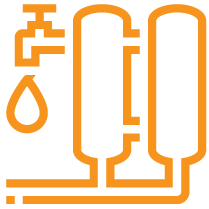
Conventional lime treatment
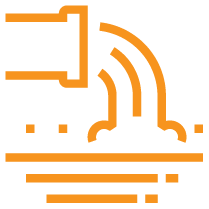
High-density sludge treatment
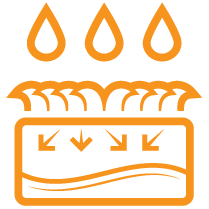
Unconventional direct acid rock drainage feed to membrane systems
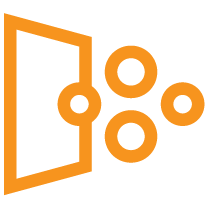
Nanofiltration

Active media filtration
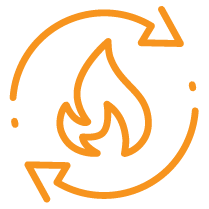
Cyanide detoxification processes
The process model output includes aqueous and solids phase compositions of major streams and is capable of interfacing the volumetric recoveries and mass removal efficiencies with the client’s site-wide water balance model or GoldSim model. This allows trade-off studies to evaluate different water treatment facility capacities and technology options to control site storage volumes over short- and medium-term projections.
Our methodology enables us to advise you on the most appropriate technology to minimise capital and operational expenditure. By combining advanced solutions and expertise, we gain a holistic understanding of your site’s water requirements and challenges, enabling us to determine the best approach.
We have a technology-agnostic philosophy and will therefore provide a solution that is unbiased to proprietary offerings.
Technology Solution
Advanced Chemical Modeling
At Miwatek, we have developed proprietary chemical modelling to enable the accurate prediction and implementation of site-specific solutions. We update these models regularly with calibrated data from our operational facilities. Using ASTM D4194-03, our in-house laboratory can determine membrane performance under various site condition predictions and then select the most appropriate membrane.
Our ability to model water treatment plants theoretically is world-class. This model uses PHREEQC to perform aqueous geochemical calculations combined with chemical unit operations such as Ultrafiltration, Reverse Osmosis, Reactors, and Cyanide Destruction Units.
Technology solution
Portfolio
Pre-engineered mobile multimedia filtration (MMF) and reverse osmosis (RO) plants:
Our pre-engineered mobile MMF and RO system is deployable without an MMF feed tank or an RO feed tank. Minimal site installation is required, and HDPE polytanks can be used for other tankage requirements. This solution is cost-effective and easily deployable.
Reference:
- Akyem (60L/s mobile plant)
Simplified brine treatment:
If simplified brine treatment is required for sulphate reduction and partial recovery of primary RO brine, then we have a process that eliminates the need for a thickener and still achieves high solids loadings in the reactor for effective sulphate reduction and scale control.
References:
- 180 m3/h primary RO with simplified brine treatment, Newmont Ahafo, commissioned October 2017 and still operated and maintained by Miwatek
- 270 m3/h primary RO with simplified brine treatment, Newmont Akyem in Ghana, commissioned May 2022 and operated and maintained by Miwatek
High overall recovery RO and brine treatment:
If the minimisation or elimination of effluent stream is required, we have process solutions that include primary reverse osmosis followed by gypsum and calcite precipitation. A treated brine recycle can be employed, and with our advanced modelling capability, we are able to define the sensitivities and accurately determine the overall volumetric recovery possible.
References:
- CC&V tunnel
- VHL
Direct acid rock drainage feed to ultrafiltration and reverse osmosis:
Substantial Capex and Opex savings are possible in the treatment of low pH acid rock drainage using unconventional acid UF and acid RO technology to pre-concentrate the feed to a high-density sludge (HDS) process on brine treatment. The solids formed parameter of HDS is improved, leading to better thickener loading rates, and the HDS facility becomes the brine treatment facility for the RO component.
References:
- Pilot study for Newmont Yanacocha
- Feasibility engineering for Newmont Yanacocha